Окончательная обработка
После окончания этой обработки изделия выдерживают в открытых автоклавах до тех пор, пока разность температур в автоклаве и вне его станет меньше 30° С. Затем вагонетки выкатывают, формы разбирают и направляют на пункт очистки для последующего использования. Готовые изделия маркируют и транспортируют на склад.
При изготовлении силикатобетонных плит необходимо соблюдать правила техники безопасности, общие для всех производственных предприятий заводского типа и, кроме того, те, которые предписаны для эксплуатации автоклавов. Давление пара в автоклаве не должно превышать предельного, указанного в паспорте и разрешенного котлонадзором. Управлять работой автоклавов могут только лица, сдавшие специальные экзамены и имеющие соответствующие удостоверения. Нельзя допускать присутствия вблизи автоклава лиц, не имеющих отношения к его эксплуатации.
Изготовление шлаколитных плит осуществляют на территории металлургических заводов (или вблизи них) способом отливки. При этом сборно-разборные металлические формы заполняются огненно-жидким Шлаком.
Физико-механические свойства литых шлаковых изделий колеблются в значительных пределах в зависимости от химического и минералогического составов шлака, а также и от технологии производства работ и в первую очередь от теплового режима отливки и остывания изделий. Как правило, прочностные свойства выше у шлаков, обладающих высокой плотностью. Так, для шлаков с объемным весом кусков более 2,6 гсмг пределы прочности при сжатии составляют от 800 до 2360 кгсм2, а при изгибе — от 60 до 370 кгсм2. Пористость кусков плотного шлака достигает
7—11%, но в то же время он обладает высокой морозостойкостью. Шлаковый щебень выдерживает 100—200 циклов попеременного замораживания и оттаивания, а шлаковая брусчатка в ряде случаев не имеет признаков разрушения после 80 лет службы. Последнее в значительной степени объясняется образованием на поверхности литых шлаковых изделий слоя повышенной плотности толщиной 2—3 мм, защищающего изделие от проникания воды.
В зависимости от теплового режима изготовления литые шлаковые изделия имеют мелкокристаллическую, крупнокристаллическую или стекловидную структуру. Иногда шлак в одном изделии имеет смешанную структуру. При этом в поверхностных слоях обычно преобладает стекловидная структура.
Наиболее высокие показатели прочности имеет шлак мелкокристаллической структуры. Стекловидный шлак отличается хрупкостью, плохо сопротивляется ударам, износу, изгибу.
Технологический процесс изготовления плит сборных покрытий и оснований дорожных одежд способом отливки из огненно-жидких шлаков состоит из следующих основных операций: подготовки форм, заполнения их огненно-жидким шлаком, выдерживания заполненных форм (остывание изделий), разборки их и транспортировки готовых изделий на склад.
Наиболее ответственной операцией, определяющей структурообразование остывающего шлака и, следовательно, его физико-механические свойства, является выдерживание заполненных форм. Создание мелкокристаллической структуры шлака обеспечивается медленным и относительно равномерным по всей толщине плиты остыванием. При быстром остывании шлак приобретает стекловидную структуру и качество изделия резко снижается. Обеспечить оптимальный режим остывания тем труднее, чем крупнее изделие. Чтобы снизить скорость остывания огненно-жидкого шлака в формах, их укрывают защитным слоем из этого же шлака.
Требования к режиму выдерживания заполненных форм должны быть учтены заранее, при подготовке форм к заполнению огненно-жидким шлаком. Для отливки шлаковых изделий используют сборно-разборные формы из листовой стали толщиной. 6—10 мм. Их устанавливают в литейных ямах, расположенных рядами вдоль железнодорожного пути, по которому подают для слива шлаковоз-ные ковши, заполненные огненно-жидким шлаком (103). Размеры каждой литейной ямы примерно 3X5 ж в плане, глубина 0,6 м. При таких размерах каждая яма может быть заполнена огненно-жидким шлаком из одного стандартного шлаковозного ковша. При другой емкости ковша или при производстве отливок в несколько ярусов в одной яме размеры ее соответственно изменяют.
На дне литейной ямы устраивают слой основания из шлакового щебня толщиной около 5 см. Поверх шлакового щебня отсыпают выравнивающий слой (1—2 см) из шлаковых высевок или кварцевого песка. Назначение этого основания— предохранять снизу формы с горячим шлаком от быстрого остывания, а также отводить попадающую в ямы дождевую воду.
Для изготовления небольших блоков типа брусчатки используются формы без дна. При этом непосредственно на выравнивающий слой основания литейной ямы устанавливают сборные стенки и накрывают их крышкой с отверстиями. Диаметр отверстий 30—35 мм, количество — примерно 20 шт. На 1 м2 поверхности крышек.
Огненно-жидкий шлак сливают из железнодорожного шлаковоз-ного ковша в литейную яму. Через отверстия в крышках форм он заполняет их полностью и, кроме того, разливается поверх форм, образуя верхний защитный слой.
В огненно-жидких шлаках всегда имеются газы. Количество их зависит от химического и минералогического составов шлаков. В период остывания большая часть газов выделяется из шлака в атмосферу. Выход газов из шлаков, находящихся в формах, происходит тоже через отверстия в крышках. При большой газонасыщенности в защитном слое, а иногда и в верхней части отливок образуются газовые раковины, наличие которых существенно ухудшает качество изделий. Образование раковин в отливках сопровождается неравномерным поднятием их поверхности (пучением). Значительно уменьшить эти процессы можно путем укладки на крышки форм тяжелых грузов (рельсов, металлических отливок).
Tweet
Формование плит< Предыдущая | Следующая >Формы для отливки крупных изделий |
---|
Поиск по сайту
Стройматериалы
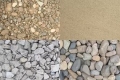
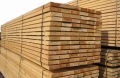
