Формование плит
Формование плит производят в металлических разборных формах. Подача готовой смеси в формы должна быть организована таким образом, чтобы от момента выхода ее из смесителя до укладки проходило не более 15 мин для смесей с вяжущими, приготовленными на основе извести-кипелки, и не более 30 мин для смесей с вяжущими на основе гидратной извести.
Подготовку форм к укладке смеси производят так же, как и при изготовлении железобетонных изделий. Их тщательно очищают металлическими щетками и сильной струей воды от пыли, грязи, остатков старого бетона. Внутреннюю поверхность форм для уменьшения сцепления их с бетоном смазывают различными минеральными маслами, нигролом, мазутом, масляным гудроном и т. Д. В результате смазки на внутренней поверхности форм должна образоваться сплошная тонкая пленка толщиной 0,2—0,5 мм. Смазка форм может быть заменена обклейкой винипластовой фольгой.
При изготовлении армированных плит после смазки форм в них укладывают арматуру в виде готовых каркасов, отдельных стержней или тонкой проволоки. Требования к арматуре сохраняются такие же, что и при изготовлении армированных конструкций из обычного бетона. Для защиты от коррозии ее покрывают антикоррозийными обмазками, затем крепят к стенкам форм и укладывают йа специальные подставки из обрезков арматуры таким образом, чтобы предотвратить возможность смещения при укладке смеси в формы.
Смесь, уложенную ib форму, уплотняют вибрированием, используя виброплощадки типа СМ-468У, СМ-176У, СМ-867 и т. Д. Рекомендуется такой режим вибрирования, при котором обеспечивается частота колебаний порядка 2800—3000 колмин и амплитуда 0,3—0,8 мм. Степень уплотнения повышают, применяя дополнительный пригруз от 50 до 100 гсм2.
Для повышения качества ровности и плотности дорожных покрытий их обычно формуют лицевой поверхностью вниз. Вначале укладывают примерно 20% общего количества смеси, вибрируют ее в течение 30—40 сек, затем полностью заполняют форму, устанавливают подрессоренную пригрузочную плиту и продолжают вибрирование в течение 2,5—3,0 мин. Такой порядок укладки и уплотнения обеспечивает хорошее заполнение углов формы и повышенную плотность поверхностного слоя плиты.
Можно изготовлять также двухслойные плиты из материалов различной крупности. Обычно верхний слой (слой износа) толщиной около 5 см устраивают из крупнозернистой смеси и нижний слой — из мелкозернистой. В этом случае вначале отдельно укладывают и уплотняют крупнозернистую смесь, а затем мелкозернистую. Режим уплотнения такой же, что и описанный ранее. После уплотнения обоих слоев плита должна представлять собой плотный монолит.
Сформованные изделия подвергают тепловлажностной обработке в автоклавах. До начала автоклавной обработки должен полностью закончиться процесс гашения извести в известково-песчаной емеси. В противном случае, т. Е. При гашении в автоклаве, известь набухает и деформирует изделия. Поэтому при использовании для помола негашеной извести рекомендуется выдерживать изделия перед направлением в автоклавы в течение 2—4 ч.
Автоклавы представляют собой горизонтально лежащие цилиндры с герметически закрывающимися крышками в торцах. Обычно их устанавливают комплектами из нескольких цилиндров. Количество цилиндров в комплекте определяется мощностью завода. К каждому цилиндру подходит рельсовый путь, который продолжается и внутри автоклава. По этим путям в автоклавы подают вагонетки с заполненными формами.
Формы с заполненными изделиями (плитами) укладывают в автоклаве друг на друга в несколько ярусов с просветами между ними по высоте (102). Такие просветы нужны для того, чтобы пар лучше обогревал каждую форму со всех сторон. Создают их при помощи укладки форм на специальные подкладки.
Цилиндрическая форма автоклавов неудобна для размещения крупногабаритных плит, но она наиболее целесообразна для восприятия внутреннего давления пара.
Выпускаемые промышленностью автоклавы в большинстве случаев рассчитаны на рабочее давление пара 8—12 ати и температуру нагрева до 200° С. Режим автоклавной обработки зависит от размеров изделий, применяемых материалов, особенностей форм и других местных условий. Обычно . Предварительно его намечают по справочным данным, а затем уточняют опытным путем. Союздорнии для дорожных плит толщиной до 20 см рекомендует следующий ориентировочный режим автоклавной обработки ( 35).
Особенно тщательно необходимо контролировать равномерность повышения и понижения давления пара и соблюдение заданной длительности этих процессов. Ускоренный или неравномерный впуск и
Особенно выпуск пара может вызвать появление существенных дефектов в изделиях, в связи с возникновением значительных перепадов давления и температуры внутри изделия и на его поверхности. Изделие в автоклаве может быть повреждено также конденсатом. Температура пара, впускаемого в автоклав, в начале обработки всегда выше температуры изделий, форм и стенок автоклава.
От соприкосновения с более холодными поверхностями начинает охлаждаться и конденсироваться. Этот процесс продолжается до тех пор, пока температура всех поверхностей (изделий и автоклава), соприкасающихся, с паром, станет одинаковой с температурой пара. Конденсат собирается в капли на стенках автоклава и форм изделий. Количество его значительно, поэтому постепенно на дне автоклава скапливается некоторое количество воды. Наиболее отрицательно действуют капли конденсата, падая на расположенные ниже плиты. Если изделия имеют открытые поверхности, то конденсат может существенно повредить их. Для защиты от падающих капель рекомендуется покрывать плиты сверху металлическими листами (см. 102), крафтбумагой и т. Д.
Tweet
Изготовление силикатобетонных плит< Предыдущая | Следующая >Окончательная обработка |
---|
Поиск по сайту
Стройматериалы
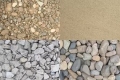
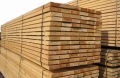
